«РАДОН» на «Фабрике процессов»




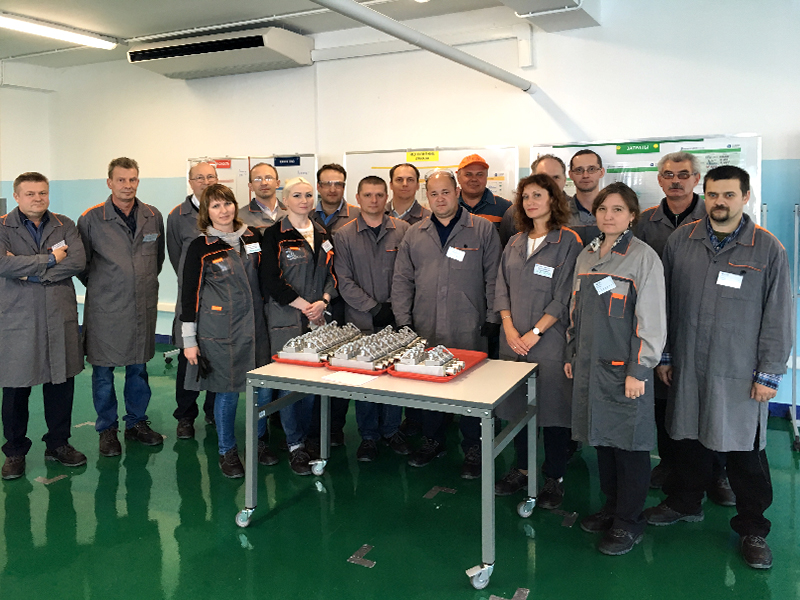
Представители ФГУП «РАДОН», ФГБНУ ВНИИФ, ОДЦ УГР, АО «Концерн Росэнергоатом», АО «РУСБУРМАШ» приняли участие в обучении производственной системе «Росатома» (ПСР). Эксперты Академии «Росатома» представили гостям один из самых востребованных в отрасли форматов обучения ПСР – «Фабрику процессов». Учебная площадка, расположенная на территории АО «Московский завод полиметаллов», позволила имитировать реальные условия производства.
Чтобы понять суть бережливого производства, участники должны были полностью погрузиться в производственный процесс. На восемь с половиной часов они перевоплотились в работников завода, куда поступил заказ на изготовление партии коллекторов для разделения изотопов урана. Участники прожили три условных смены, за каждую из которых нужно было выпустить десять деталей надлежащего качества, сократить рабочую площадь, перестроить линию производства, уменьшить себестоимость единицы продукции, снизить запасы и перераспределить между собой роли директора, менеджера по труду, менеджеров по улучшениям, логиста, контролера ОТК, операторов.
Одним из главных условий работы было соблюдение правил техники безопасности. Поэтому фиксировались любые нарушения: работа без средств индивидуальной защиты, складирование тары в несколько ярусов, использование телефонов и др.
Итоги трёхсменной работы были таковы: в первую смену выпустили две детали, во вторую – четыре, а в третью план был даже перевыполнен – одиннадцать деталей вместо десяти.
Каждый участник на реальном производственном процессе получил практический опыт применения следующих ключевых инструментов ПСР: поток создания ценностей, поток единичных изделий, сбалансированная работа, виды потерь, система 5С, визуализация и операционные показатели деятельности.
Прямая речь:
Антон Андреев, начальник технического бюро цеха по перевозке РАО и механизации РРР.
У нас, людей из различных организаций и предприятий, была общая цель и ответственность за результат. В кратчайшие сроки группа совершенно незнакомых людей в «боевых условиях» сумела сплотиться для достижения поставленной задачи. Разбирая полеты, мы поняли, что начинать работу надо не с увеличения ресурсов, а с анализа процесса и поиска потерь, которые, в конце концов, нами были устранены. При грамотном подходе руководства к управлению процессом производства продукта, можно достичь любых показателей с минимальными затратами.
Василий Андресов, начальник участка приема, кондиционирования и хранения РАО цеха по обращению с РАО.
Нашей задачей было найти моменты, в которых можно было что-то улучшить. Сделать так, чтобы процесс стал более экономичным и в то же время компактным. Помимо нестандартного, но эффективного обучения на «Фабрике процессов» подавали замечательные ланчи.
Наталья Титова, начальник производственно-технического отдела.
«Фабрика процессов» – это уникальная обучающая площадка, где мы не просто слушали и конспектировали, но и применяли полученные знания на практике, видели, как наши определенные действия влияли на производственную картину и отражались на деньгах.
Андрей Юрченко, начальник участка по переработке РАО цеха по обращению с РАО.
Конечно, были споры насчёт того, как что-то улучшить, изменить. В конечном итоге, с поставленной задачей мы справились. Но самым главным и серьёзным результатом стало не это. А то, что мы научились по-другому смотреть на своё дело. И в процессе игры обнаружили ошибки, которые совершаем в своей работе в реальной жизни.
Леонид Колосницын, начальник участка по переработке металлических РАО цеха по обращению с РАО .
Было очень интересно и увлекательно оказаться в сообществе незнакомых людей, объединившихся ради выполнения общей задачи. К концу тренинга мы поняли, что не процесс управляет нами, а мы управляем процессом.
Тимофей Ермаков, руководитель программ ПСР Центра обучения Производственной системы «Росатома» АНО «Корпоративная Академия Росатома».
Главная цель «Фабрики процессов» – изменение представления о традиционных подходах к управлению производством, другими словами, формирование ПСР-мышления. Важная задача участников после обучения – переложить опыт оптимизации процесса на свои основные задачи и процессы, то есть увидеть и устранить потери, сбалансировать процесс и выстроить поток создания ценности. Ведь независимо от особенностей наших предприятий все мы имеем дело с процессами, которые возможно и необходимо улучшать.